Respect for Human Rights at Ryohin Keikaku
Monitoring Production Partners
Ryohin Keikaku, in collaboration with our business partners, conducts monitoring of production partner factories (hereinafter referred to as "factories") based on the "Code of Conduct for Production Partners." This aims to fulfill our social responsibility by actively promoting respect for human rights, compliance with labor-related laws, improvements in working conditions, and environmental sustainability in our supply chain.
■Monitoring of the Working Conditions
Ryohin Keikaku does not own any production plants or production facilities, nor do we manufacture any products. All product manufacturing is subcontracted to factories in Japan and other various countries and regions.
Based on reports from international organizations and NGOs, as well as our past experiences, we recognize the high level of human rights risks in our supply chain and are committed to engagement with factories to prevent and mitigate negative human rights impacts. As part of our engagement with factories, we conduct regular on-site audits by a third-party organization, based on the "Code of Conduct for Production Partners," covering aspects such as human rights violations, labor conditions, and environmental impact.
Since 2016, we have also incorporated audits conducted under the Better Work programme, a joint activity program by the International Labour Organization (ILO) and the International Finance Corporation (IFC). Better Work audits, which are widely adopted in the apparel industry, reduce the duplication of factory audits and enable factories to focus more on improving working conditions.
■Factory Monitoring
Factory monitoring framework
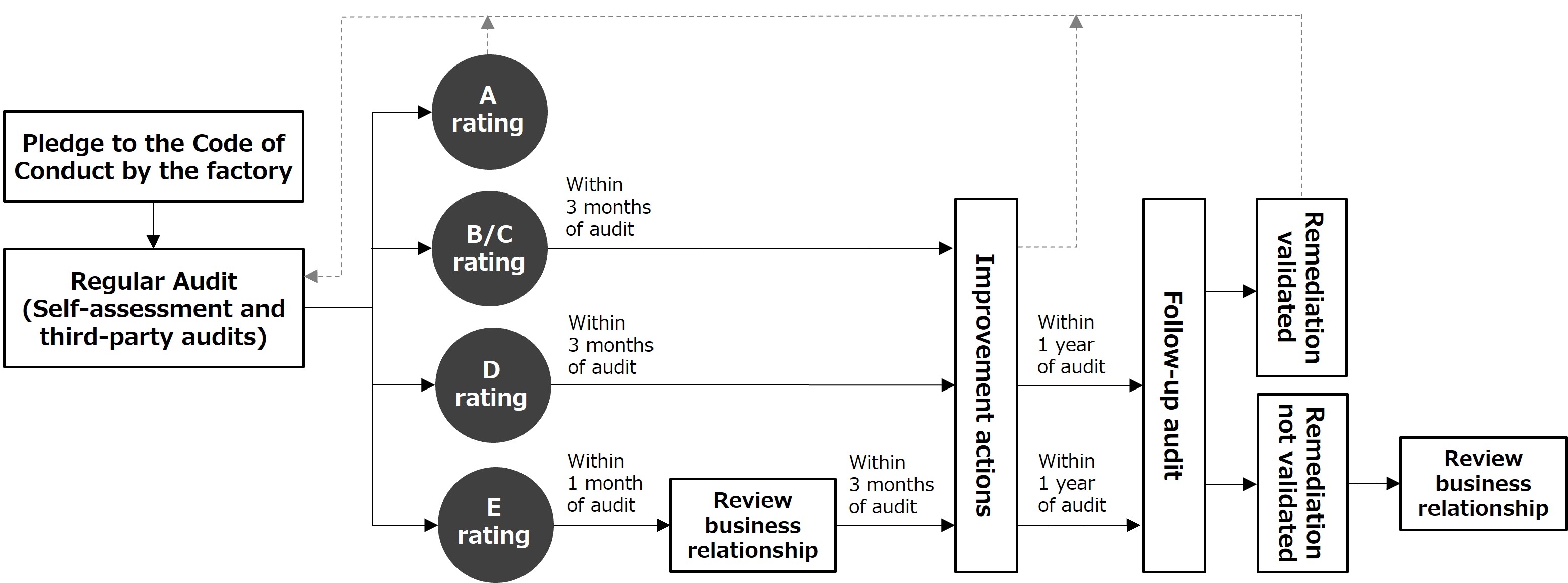
*The evaluation and improvement process of factories that participate in the Better Work assessment program may differ from the above.
Audit items
Ryohin Keikaku, in collaboration with a third-party auditing organization, has established its own audit items based on the "Code of Conduct for Production Partners" and various ILO conventions.
Classification of audit items:
Child labor and young workers, forced labor, terms of employment, health and safety (fire safety, building safety, machinery safety, electrical safety, chemical management, occupational health and safety, personal protective equipment, workplace accidents, first aid, dormitories and canteens), freedom of association, discrimination, disciplinary actions, working hours, wages and compensation, monitoring and compliance, corporate ethics (anti-bribery, management systems), procurement management, environmental management
Assessment method
Since 2019, Ryohin Keikaku has been conducting audits through a third-party organization for factories that are not subject to the Better Work program. Audits are generally conducted once every two years for all Tier 1 factories. During the audit, auditors visit the factory to review records and documents such as labor contracts, pay slips, work records, and timecards, and to confirm occupational health and safety conditions through on-site inspections. They also conduct interviews with factory employees (without management present) as well as management. If dormitories are provided, these are also inspected to ensure adequate living space, proper hygiene management, and other necessary conditions.
From 2023, third-party on-site audits have been gradually extended to Tier 2 factories that supply apparel and textile products. The audit items and assessment methods are the same as those applied to Tier 1 factories.
Risk assessment
Ryohin Keikaku rates factories on a five-point scale from A to E, based on the severity and number of findings in the audit results, as an indicator of human rights and environmental risk at the factories.
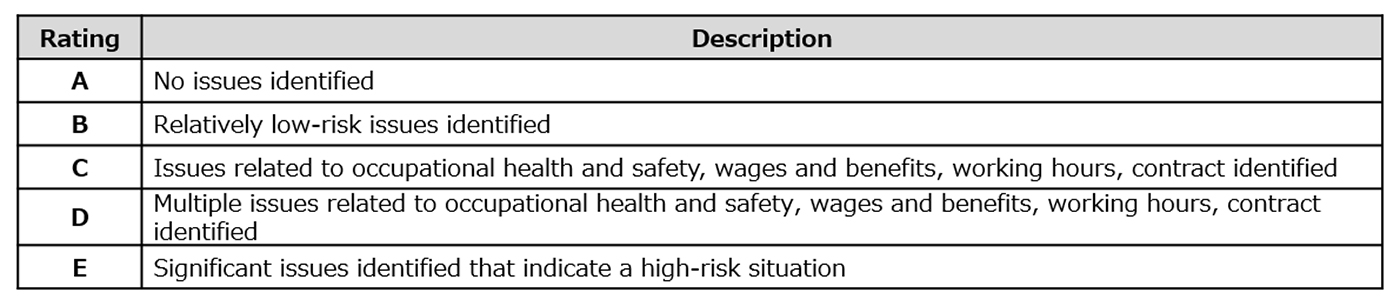
Corrective action
Ryohin Keikaku provides feedback to factories on identified issues and risk assessment results requesting factory management to implement improvements while offering support to facilitate the corrective process. Based on improvement reports prepared by factories, Ryohin Keikaku works with factories to identify root causes, such as specific activities/procedures or lack thereof, that led to the issues. We also assess whether systemic changes are necessary to prevent recurrence.
For factories where the risk assessment has been rated as D or E through the audit, follow-up audits will be conducted focusing on the issues identified. If the remediation of identified issues is not validated during follow-up audits, Ryohin Keikaku will carefully review the possibility of reassessing the business relationship in meetings attended by inside directors, taking into account the factory's management and employment conditions. If, as a result of human rights due diligence throughout the supply chain, including on-site audits, serious human rights violations are confirmed, and if corrective action cannot be expected even if Ryohin Keikaku exerts its influence, the termination of the business relationship with the factory will be considered as an option in accordance with the "Code of Conduct for Production Partners."
Factory Monitoring Results
Please refer to the report below for the audit results of the factories for FY2024.
■Subcontracted Factories Monitoring
Under the "Code of Conduct for Production Partners," Ryohin Keikaku prohibits production partners from subcontracting to factories without Ryohin Keikaku's prior approval. Additionally, when subcontracting production to other factories, production partners must ensure the subcontracted factories' business practices comply with the "Code of Conduct for Production Partners."